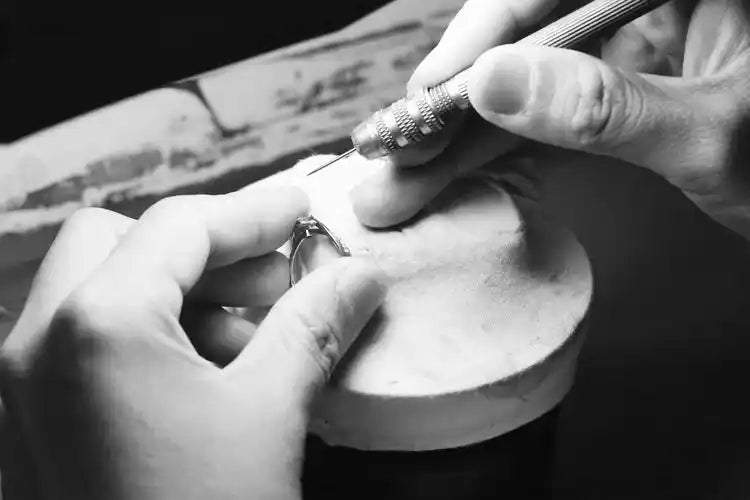
In the world of fine jewelry, S925 gold-plated pieces have long been prized for their elegant blend of sterling silver durability and luxurious gold finish. But behind their timeless shine lies a revolution in manufacturing—one focused on low-carbon processes and energy-saving technologies that enhance both quality and sustainability. This shift isn’t just about environmental responsibility; it’s about crafting jewelry that lasts longer, shines brighter, and meets the evolving expectations of discerning consumers. Let’s explore the innovative techniques transforming S925 gold-plated jewelry production.
Low-Carbon Materials: The Foundation of Sustainable Craftsmanship
1.Recycled Sterling Silver Takes Center Stage
S925 silver (92.5% pure silver, 7.5% alloy) is now increasingly sourced from post-consumer recycling rather than virgin mining:
Closed-Loop Recycling: Brands like Pandora and Brilliant Earth melt down old jewelry, medical devices, and even solar panels to create new S925 alloys, reducing energy use by 95% compared to mining . This process yields silver of the same purity and malleability as mined silver, ensuring no compromise on craftsmanship.
Alloy Innovation: Recycled silver is paired with recycled copper or zinc (instead of nickel) to create hypoallergenic blends, improving wearer comfort while diverting industrial waste from landfills.
2. Efficient Gold Plating with Minimal Waste
Gold plating, a critical step in S925 jewelry production, now uses ultra-thin layers (2.5–5 microns) and advanced material recovery:
Precision Electroplating: New generation machines (e.g., Voyageur Plating Systems) use pulsed current to deposit gold evenly, reducing overplating by 30% and ensuring a more durable bond with the silver base.
Gold Reclamation: Spent plating solutions are processed via ion-exchange technology, recovering 99.9% of unused gold for reuse—eliminating waste and preserving this precious resource.
Energy-Saving Technologies: Powering Production Responsibly
1. Smart Heating Systems for Casting & Polishing
The high-temperature processes in jewelry making (casting at 800–900°C, polishing) are now optimized for efficiency:
Induction Heating: Replacing traditional gas furnaces, induction systems heat silver alloys 30% faster with 70% less energy, thanks to magnetic field technology that targets material directly.
LED-Cured Finishing: In polishing and coating stages, LED UV curing reduces energy use by 50% compared to traditional UV lamps, while delivering a harder, more scratch-resistant gold-plated surface.
2. 3D Printing for Zero-Waste Design
3D powder-bed fusion technology is revolutionizing jewelry prototyping and production:
Material Efficiency: 3D printers use 98% of input silver powder, with unused material recycled back into the system—eliminating the 15–20% waste typical of traditional casting methods.
Design Freedom: Intricate geometric patterns and lightweight structures, previously impossible to craft by hand, are now achievable with minimal energy, expanding creative possibilities for S925 gold-plated jewelry.
Waste Management: Turning Byproducts into Value
1. Water Recycling in Plating & Cleaning
Plating and cleaning processes, once major sources of water waste, now feature closed-loop systems:
Reverse Osmosis Purification: After gold plating, wastewater is filtered through RO membranes, removing 99% of contaminants (including trace gold particles) and recycling 80% of water for reuse.
Ultrasonic Dry Cleaning: Cutting-edge facilities use waterless ultrasonic technology to remove oils and debris from jewelry surfaces, eliminating the need for harsh chemicals and reducing water consumption by 90% compared to traditional methods.
2. Metal Shavings & Dust Recovery
Even the smallest byproducts are now valued:
Vacuum Collection Systems: During machining and polishing, the finest silver shavings and gold dust are captured and re-smelted, ensuring 95% of workshop waste is returned to the material supply chain.
Mold Material Innovation: Biodegradable, plant-based binders (replacing petroleum-derived compounds) used in casting dissolve harmlessly, leaving no toxic residue and reducing solid waste by 30%.
The Future of Jewelry Manufacturing is Efficient—and Brilliant
The journey of S925 gold-plated jewelry from raw material to finished piece is now a story of innovation as much as artistry. By embracing low-carbon materials, energy-saving technologies, and smart waste management, manufacturers are creating jewelry that’s not just beautiful, but built to last—both in your collection and in the world.
Explore our S925 gold-plated jewelry collection, crafted using the latest energy-efficient processes to deliver enduring shine and quality. Every piece is a testament to what happens when craftsmanship meets ingenuity. 🌟